CRC Concrete Raising Corporation offers the services of concrete raising, void filling and/or soil stabilization, cement grouting and concrete replacement.
Should you have any questions...
Concrete Raising
CRC Concrete Raising Corporation uses a calibrated cementitious grout (or slurry) to raise slabs and fill the voids beneath them. This process of raising concrete with concrete results in a repair that is impervious to water, and therefore a more permanent fix than other common methods. So permanent, that warranties for work done via the calibrated CRC method often exceed warranties provided for new concrete by two-to-four (2-4) times.

The cementitious grout is pumped under pressure via small holes (generally less than two-inches in diameter) drilled through the concrete slabs. The grout displaces air pockets, water, and water-saturated materials, effectively stabilizing the sub-base or subgrade to provide uniform support. The CRC method raises the slab, filling the voids beneath the slab, and providing for a firm, more-permanent subgrade.
What Can Be Raised By Concrete Raising?
CRC Concrete Raising Corporation can raise, level, and stabilize: sidewalks, driveways, garage floors, patios, pool decks, steps, stoops, curb and gutter, concrete pavement (streets, highways, interstates), bridge approaches, industrial floors, parking lots, airport runways, and building foundations.
In essence, virtually any slab-on-grade concrete within a residential, commercial, industrial, or municipal/State DOT setting, can be raised back to its original grade.
Why Consider Concrete Raising?
The cost to raise existing concrete is often one-third to one-half (1/3 to 1/2) the cost of replacement (varies by location & job type).
If the concrete is structurally sound, and the concrete has settled… why not address the actual cause of the settlement (the sub-base or the subgrade)?
Void Filling
CRC Concrete Raising Corporation uses a calibrated cementitious grout (or slurry) to fill voids through injection ports (generally less than two-inches in diameter) drilled through concrete slabs. The grout displaces air pockets, water, and water-saturated materials, effectively stabilizing the sub-base or subgrade to provide uniform support. The CRC method fills the voids beneath the concrete, providing for a firm, more-permanent subgrade.
The service of void filling and/or soil stabilization is often viewed as a preventive treatment. Concrete areas that feel/sound “hollow”, abandoned sewer and/or water lines, utility trenches, flood plain areas subject to erosion, and poorly-compacted soils around foundations, abutments, and retaining walls are just some of the common areas in need of void filling by way of a calibrated cement grout.
Basement Repair
CRC Concrete Raising Corporation provides basement repair services at a variety of CRC locations – consult your local CRC Concrete Raising location for service availability.
Wisconsin basement repair service provided:
Basement Crack Repair: CRC Wisconsin provides basement “POURED” wall crack repairs. We use multiple types of resins to inject cracks, holes, and other porous areas. Exclusively-formulated products are used to permanently waterproof and/or repair your concrete foundation issues.
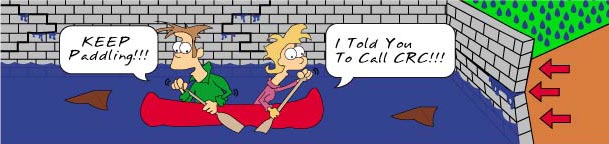
Types of Cement Grouting
Pressure Grouting: closely related to concrete raising, and performed using the same equipment, with the addition of a nozzle extension. Commonly referred to as soil stabilization, pressure grouting is a form of permeation grouting, and is an economical means to remediate existing and potential geological and foundation support problems without causing major disruption to structures. The process consists of the direct pressure injection of a liquefied grout (usually containing microfine cement) into voids, cracks, fractures, cavities, or even between a bearing media and a structure, foundation or bearing walls. The grouting methods can take the forms of compaction, curtain, chemical, microfine cement, slurry, or any other permeation application used to install a cement grout or low-mobility material. The method requires that the media gels or solidifies within or around the treated areas: soil, pipes, cracks, fractures, conduits, or holes. The main purposes of pressure grouting are to improve support, strength, and function of a given media, element, or substance (i.e. concrete walls, pipes, blocks, gravel, cement columns, or soils).
Permeation Grouting: penetrates voids in a mass, displacing and replacing water or air between grain particles usually at low pressure to prevent fracturing. Grouts are designed and intended to “permeate the subgrade or soil” and stiffen the mass as a whole. If a cementitious grout is used, it must be thoroughly mixed with a high-shear mixer (proper functioning volumetric mixers, as modified by Concrete Raising of America, exceed high-shear capability). Chemical grouts or microfine cement grout, alone or in combination, work well for this method.
Penetration Grouting: grouting used mainly to fill joints or fractures in rock or large pore spaces in order to strengthen the existing mass and eliminate movement or water flow, without disturbing the formation. It requires a slurry mix design of water, Portland cement, fly ash, sand, or any combination thereof.
Compaction Grouting: (as defined by the Committee on Grouting of the Geotechnical Engineering Division, ASCE’s): Grout injected with less than one inch (25mm) slump, normally a soil-cement with sufficient silt sizes to provide plasticity together with sufficient sand sizes to develop internal friction. The grout generally does not enter soil pores but remains in a homogeneous mass that gives controlled displacement to compact loose soils, gives controlled placement for lifting structures, or both. Compaction grouting requires comprehensive subsurface investigation. Generally, these types of grouting jobs will incorporate a Geotechnical Engineering Consultant, whom will likely prepare an on-site investigation report and “Grout Plan” based upon site geology, history, soil gradation, and the in situ permeability (horizontal) of each stratum for treatment. Compaction grouting jobs require a contractor to directional drill for pipe placement into loose soil stratum, placement and frequency of holes for grouting are contingent upon the engineer’s Grout Plan. Grouting takes place through the pipe, and is typically performed bottom-up, but can also be top-down. Grout consistency and grouting pressure are vital to the process which will likely require a volumetric mobile mixer (on-site batching/delivery) and a pump capable of pumping a stiff grout (generally rated at 900 p.s.i. or higher).
Compensation Grouting: also known as “Fracture Grouting” involves injecting a grout slurry and hydrofracturing the soil between the foundation to be controlled and the causation of settlement. The slurry is forced into fractures, causing expansion and raising. Multiple injection locations and multiple levels of fracture(s) create a more-permanent reinforced structure. Pipe sleeves are required for various level slurry injection. Grout consistency is again vital to the overall process.
Jet Grouting: is a ground modification methodology used to create soilcrete (in situ, cemented formations of soil), which are commonly used to provide: 1. underpinning and/or excavation support; 2. Temporary/permanent stabilization of soft or liquefiable soils; or 3. Groundwater and/or underground pollution control. Jet Grouting has three traditional systems which differ by application and desired physical characteristics of the soilcrete. Typically, grout is pumped through a rod and exits a horizontal nozzle(s) at high velocity [approximately 650 ft/sec (200m/sec)]. This energy breaks down the soil matrix and replaces it with a mixture of grout slurry and in situ soil (soilcrete).
Chemical Grouting: within the industry, there are two (2) classifications of chemical grouting: structural and water control. Structural-the permeation of sands with fluid grouts to produce load-bearing sandstone-like masses. Water Control-the permeation of sands with fluid grouts to completely fill voids to control water flow. Typical chemical grouting agents include: Sodium Silicates, Acrylates, Acrylamides, Polyurethanes, and MC-Silicates. Seemingly the most common agents remain sodium silicate (an acrylamide generally used with a hardening agent) and polyurethanes, of which there are two (2) types: hydrophilic and hydrophobic. Hydrophilic chemical materials incorporate large amounts of water in their structure, which creates a gel. This type of material can shrink if allowed to dry. Therefore, it is vulnerable to breakdown. Hydrophobic materials use water as a reacting agent, so soil moisture content and free standing water in voids are of major concern. The cured material is essentially water free, which makes it resistant to shrinkage. This type of grouting material remains flexible and is used in moving cracks.
Concrete Replacement
CRC Concrete Raising Corporation provides concrete removal and replacement services for concrete areas that cannot be repaired by way of concrete raising due to the concrete’s lack of structural integrity.
CRC will usually prescribe the following, unless the concrete is irregular in terms of thickness and/or design, or other specifications are required:
Mix Design: CRC uses a “straight” 6-bag mix design (3,000-to-4,000 psi rating) unless otherwise stated or specified. In comparison, some contractors utilize a “Modified” design that allows for a 5-bag mix and the use of fly ash or another supplement.
“Low-Chert Aggregate”: will slightly increase the cost of materials, CRC uses “Low-Chert” to minimize the potential for “Chert-pops” or “Pop-outs”. “Chert-pops” are created when porous aggregates (a physical property of chert, a silicate with sharp edges) hold moisture, which has a tendency to freeze and expand (especially in Wisconsin winters), creating enough pressure to literally “pop-out” of the concrete. “Low-Chert” is generally 95-to-88 percent chert-free and is available through CRC’s Ready-Mix suppliers.
Wire mesh: is used unless otherwise specified by the customer, as CRC prefers the ability of the mesh to reinforce the concrete. The wire mesh is placed in a grid pattern, and is designed to add tensile strength to the concrete. Although wire mesh does not prevent cracking, it does hold the concrete together to reduce/eliminate cracks from widening and assists in preventing the concrete from settling (trip hazards, ponding water, etc.). Wire mesh is different from Fibermesh®, an additive that is used to reduce the amount of concrete cracking as a result of plastic shrinkage. Fibermesh® will increase the tensile strength of the concrete. Additionally, CRC will commonly use steel reinforcement rods when placing (or replacing) concrete adjacent to building foundations and/or garage floors to reduce the likelihood of settlement and thus pitch at/near structural areas.
Suitable Base or Subgrade: Industry standards call for a two-to-four-inch (2″-4″) minimum base of crushed rock or gravel at the location of concrete pour/placement. It is important that all organic materials are removed from the area prior to the placement of the rock/gravel and that the area be compacted properly to avoid future settlement and/or non-uniform support.
General Guidelines (Texture, Pitch, Control Joints): The Americans with Disabilities Act (ADA) Guidelines specify a surface texture and pitch to reduce slip-and-fall liability and hazardous walking environments. Most applications simply incorporate a broom-finish texture and a pitch of one-inch per four-feet (to facilitate proper water drainage). Control Joints are strategically placed by contractors such as CRC to allow for natural expansion and contraction of the concrete. Placement of the control joints varies by location (i.e. driveway control joints will be further apart than service walk control joints). These joints are designed to create low-resistance areas for hidden cracking to occur. It is the objective of each contractor to have cracks take place at the control joints so that they are not readily seen when cracking occurs.
Concrete Sealing: Concrete should be sealed after allowing for a standard cure time of twenty-eight to thirty (28-30) days to reduce the amount of water absorption. Water that penetrates and expands due to freezing damages concrete, that is, water expands approximately nine percent (9%) when it freezes, which produces enough force to break the concrete bonds and cause the concrete to “Flake”, “Pit”, “Spall”, and/or “Crack”. Not to mention the deteriorating effects moisture has on any metallic reinforcements used within the concrete for structural stability and strength. Sealing concrete, after it is clean and dry, will reduce the likelihood of water absorption, especially if a penetrating sealant (such as siloxane) is used. Reducing the absorption will also lessen some of the damaging effects of deicing salts, which melt the ice/snow initially, but allow for refreezing of moisture when the temperature drops and the deicing salt is diluted. Additional information, including but not limited to: actual concrete specifications, permits, costs, form placement and removal, re-landscaping (if needed), barricades, actual use of area, and warranties, will be provided by the CRC location providing the service of concrete replacement.
Contact CRC today for assistance in solving your concrete problems.
Snow Removal
CRC Concrete Raising Corporation provides snow plowing, snow removal, and de-icing (salting) services to managed properties including, but not limited to: condo associations, school districts, clinics and hospitals, industrial properties, retail locations, corporate offices, shopping centers, etc.
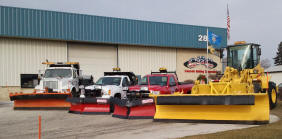
CRC maintains a variety of snow plowing and snow removal vehicles at those locations providing snow removal services.
CRC has been called upon by numerous municipalities to assist in emergency snow plowing, removal, and de-icing services after major winter storms.
Contact CRC today for assistance in solving your snow removal problems.